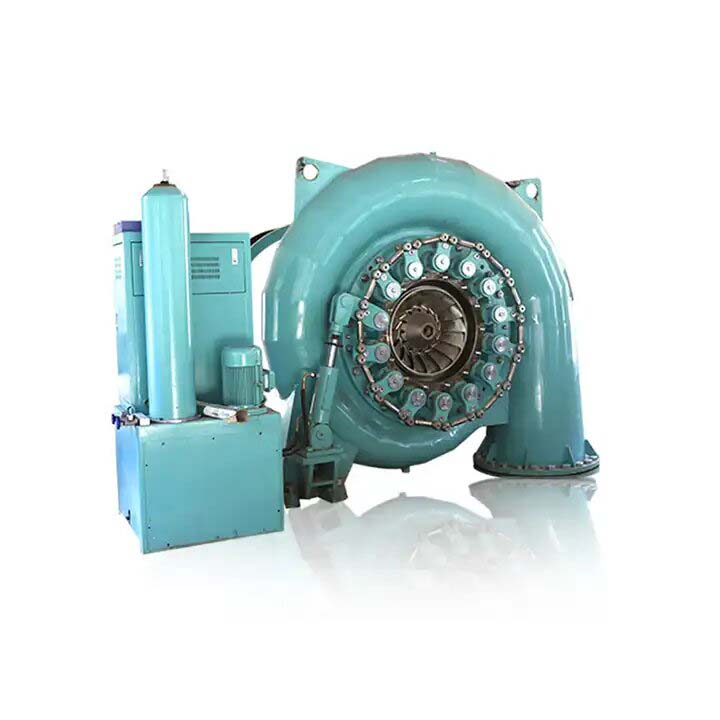
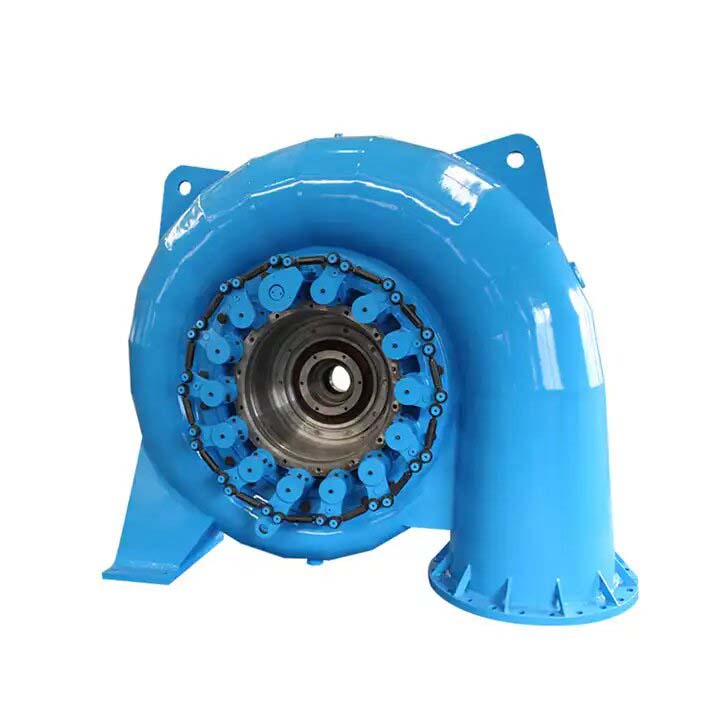
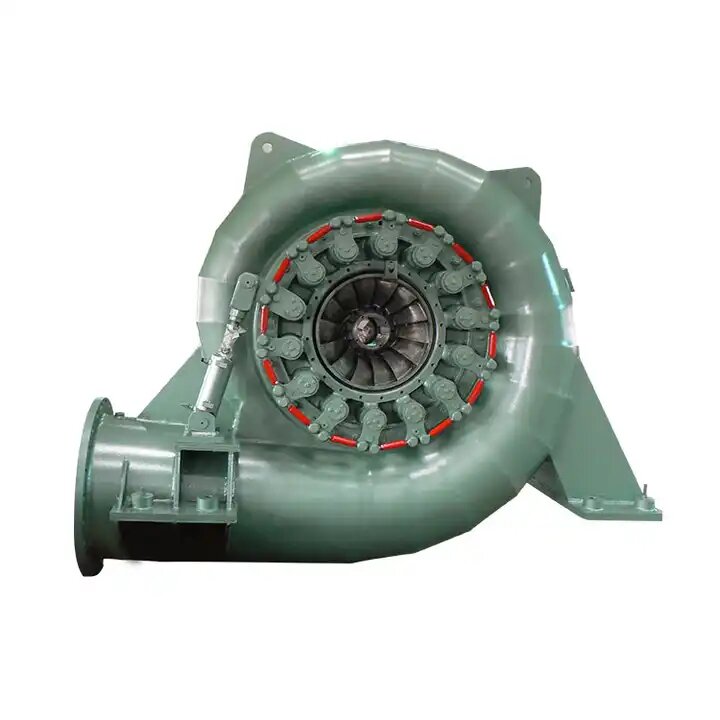
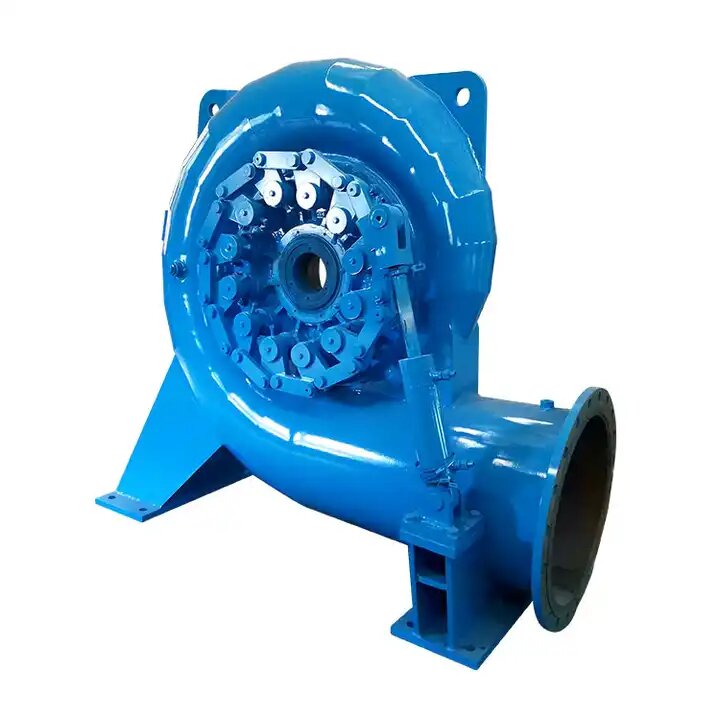
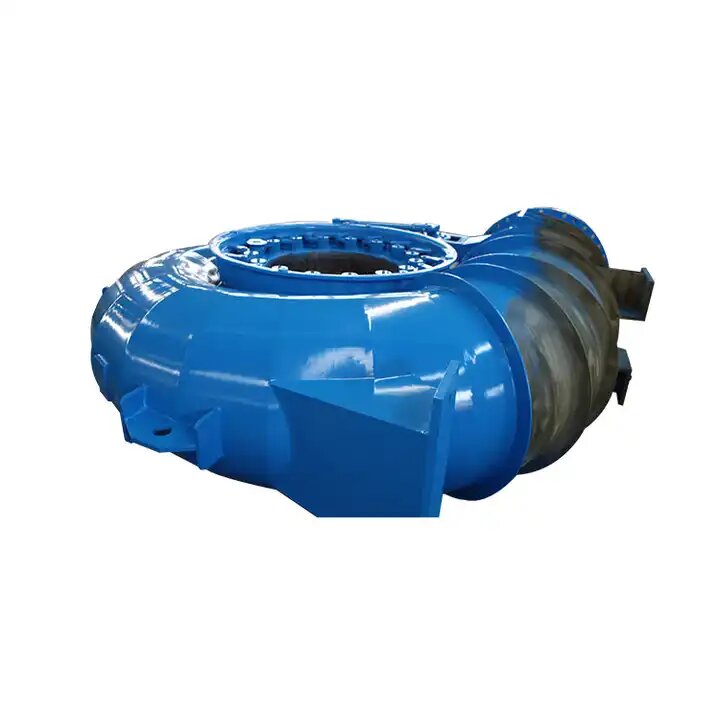
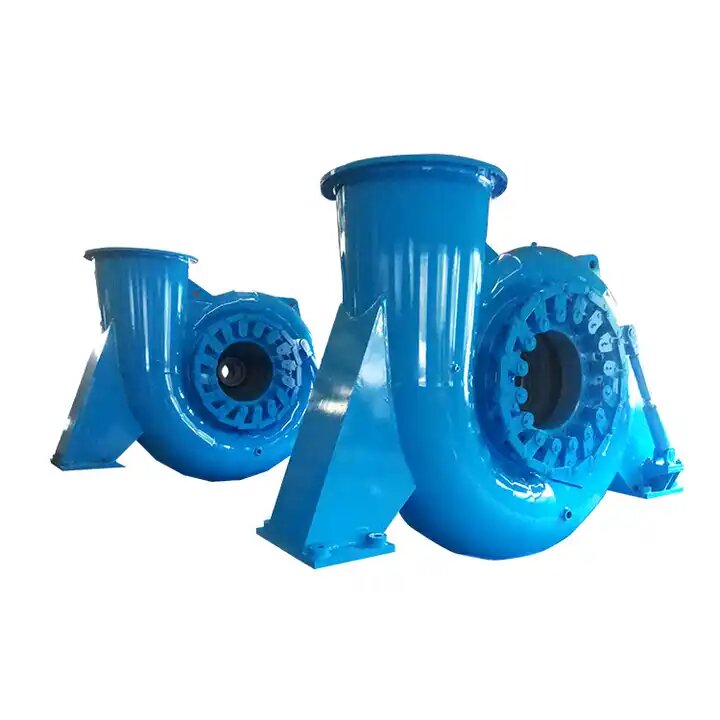
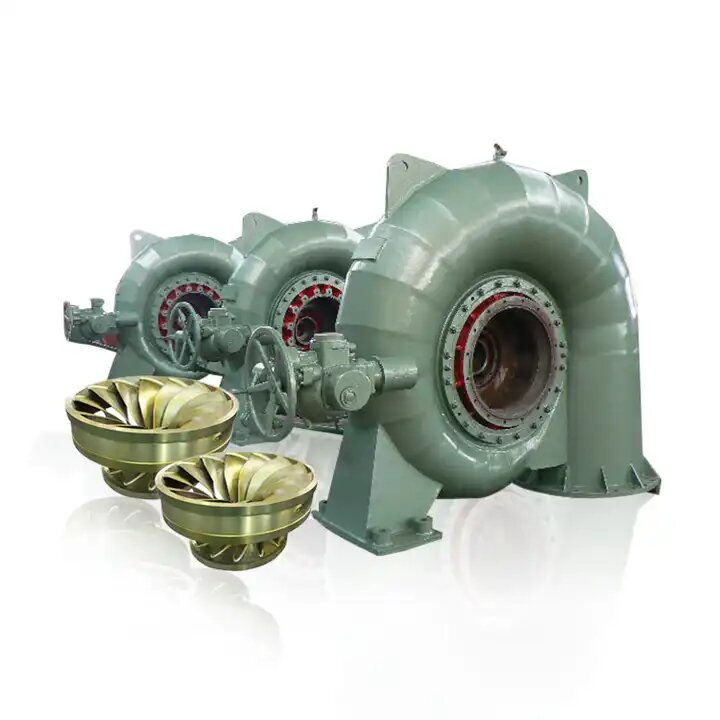
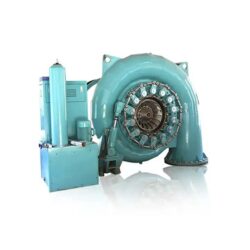
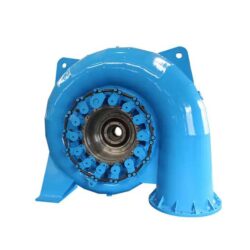
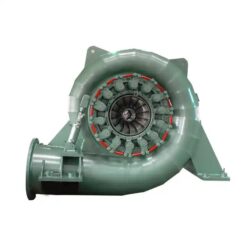
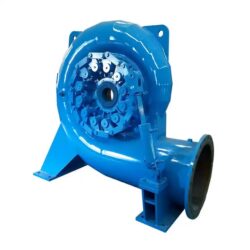
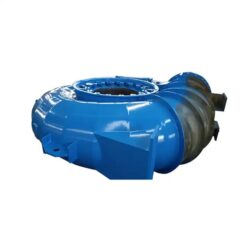
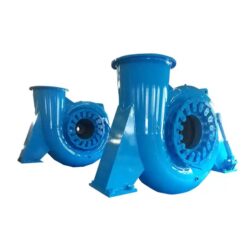
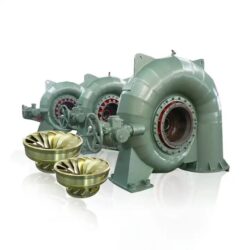
Alternative Energy Hydroelectric Generator 500kw Francis hydro turbine generator. The spiral casing is the inlet medium of water to the turbine. The water flowing from the reservoir or dam is made to pass through this pipe with high pressure. The blades of the turbines are circularly placed, which means the water striking the turbine’s blades should flow in the circular axis for efficient striking. So the spiral casing is used, but due to the circular movement of the water, it loses its pressure.
Our 500KW Francis Hydro Turbine Generators redefine hydro power with remarkable specifications.
Boasting a robust 500KW output, a flow rate of 0.83m³/s, and an impressive water head of 74.68m, these generators operate at a frequency of 50Hz. Certified with ISO9001, CE, TUV, and SGS, they adhere to the highest industry standards.
The efficiency of 93% ensures optimal energy conversion, while the brushless excitation technology of the SFW500 generator enhances reliability.
The integration of a ball valve for precise control, stainless steel for the runner material, and carbon steel for the volute material highlights the durability and advanced engineering of these hydro turbine generators.
The cost of a 500KW Francis Hydro Turbine Plant can vary significantly based on project-specific requirements and market conditions. As a rough estimate, such hydro turbine plants often range from hundreds of thousands to a few million dollars.
Factors such as the turbine's design, materials, site conditions, and additional features contribute to the overall cost. For precise pricing, consulting with Suneco hydro turbine manufacturers or suppliers is recommended, as they can provide tailored quotes based on project specifications and customization needs.
Output: 500KW
Flow Rate: 0.83m³/s
Water Head: 74.68m
Frequency: 50Hz
Certificate: ISO9001/CE/TUV/SGS
Voltage: 400V
Efficiency: 93%
Generator type: SFW500
Generator: Brushless Excitation
Valve : Ball Valve
Runner Material: Stainless Steel
Volute Material: Carbon Steel
Francis turbine definition is a combination of both impulse and reaction turbine, where the blades rotate using both reaction and impulse force of water flowing through them producing electricity more efficiently. Francis turbine is used for the production of electricity most frequently in medium or large-scale hydropower stations.
These turbines can be used for heads as low as 2 meters and as high as 300 meters. Additionally, these turbines are beneficial as they work equally well when positioned horizontally as they do when they are oriented vertically. The water going through a Francis turbine loses pressure, but stays at more or less the same speed, so it would be considered a reaction turbine.
The description of each Francis turbine’s main component diagram is as follows.
Spiral Casing
The spiral casing is the inlet medium of water to the turbine. The water flowing from the reservoir or dam is made to pass through this pipe with high pressure. The blades of the turbines are circularly placed, which means the water striking the turbine’s blades should flow in the circular axis for efficient striking. So the spiral casing is used, but due to the circular movement of the water, it loses its pressure.
To maintain the same pressure the diameter of the casing is gradually reduced, thus, uniform momentum or velocity striking the runner blades.
Stay Vanes
Stay and guide vanes guide the water to the runner blades. Stay vanes remain stationary at their position and reduces the swirling of water due to radial flow, as it enters the runner blades, thus, making the turbine more efficient.
Guide Vanes
Guide vanes are not stationary, they change their angle as per the requirement to control the angle of striking of water to turbine blades to increase the efficiency. They also regulate the flow rate of water into the runner blades thus controlling the power output of a turbine according to the load on the turbine.
Runner Blades
Runner blades are the heart of any Francis turbine. These are the centers where the fluid strikes and the tangential force of the impact causes the shaft of the turbine to rotate, producing torque. Close attention to the design of blade angles at inlet and outlet is necessary, as these are major parameters affecting power production.
The runner blades have two parts. The lower half is made in the shape of a small bucket to rotate the turbine by using the impulse action of water. While the upper part of the blades uses the reaction force of water flowing through it. The runner rotates through these two forces.
Draft Tube
The pressure at the exit of the runner of the reaction turbine is generally less than atmospheric pressure. The water at the exit, cannot be directly discharged to the tailrace. A tube or pipe of the gradually increasing area is used for discharging water from the exit of the turbine to the tailrace.
This tube of the increasing area is called Draft Tube. One end of the tube is connected to the outlet of the runner. However, the other end is submerged below the level of water in the tail-race.
Francis turbines, a staple in hydroelectric power plants, operate on a fascinating principle. The journey begins with high-pressure water entering the turbine through the snail-shell casing, known as the volute.
As the water traverses this casing, its pressure decreases while maintaining a consistent speed. Upon exiting the volute, the water encounters guide vanes, directing it towards the precisely angled blades of the runner. The runner's curved blades cause a deviation in the water's motion, diminishing its "whirl" while also deflecting it axially towards a draft tube leading to the tail race.
The strategically designed draft tube is instrumental in reducing the water's velocity, optimizing energy extraction. As water flows through the runner blades, a reactionary force is generated, propelling the blades and transmitting power to the turbine's shaft. According to Newton's third law, this reaction force facilitates the continuous rotation of the turbine. This characteristic categorizes Francis turbines as reaction turbines. Simultaneously, the alteration in water flow direction within the turbine results in a decrease in internal pressure. This intricate interplay of forces and fluid dynamics underscores the efficiency and functionality of Francis turbines in harnessing hydroelectric power.
Francis turbines are employed regularly in hydroelectric power plants. In these power plants, high-pressure water enters the turbine through the snail-shell casing (the volute). This movement decreases the water pressure as it curls through the tube; however, the water’s speed remains unchanged. Following the passing through the volute, the water flows through the guide vanes and is directed towards the runner’s blades at optimum angles. Since the water crosses the precisely curved blades of the runner, the water is diverted somewhat sideways. This makes the water lose some part of its “whirl” motion. The water is also deflected in the axial direction to exit a draft tube to the tail race.
The mentioned tube reduces the water’s output velocity to gain the maximum amount of energy from the input water. The process of water being diverted through the runner blades results in a force that propels the blades to the opposite side as the water is deflected. That reaction force (as we know from Newton’s third law) is what makes power to be carried from the water to the turbine’s shaft, continuing rotation. Since the turbine moves due to that reaction force, Francis turbines are identified as reaction turbines. The process of altering the direction of the water flow also decreases the pressure within the turbine itself.
Exemplary Technical Expertise:
Our product is backed by a distinguished technical consultant with an unparalleled 50 years of experience in the hydro turbine field. Recognized for outstanding contributions, the consultant has been honored with the Chinese State Council Special Allowance, showcasing a commitment to excellence and expertise.
This invaluable wealth of knowledge enhances our product's design and functionality, ensuring that it meets the highest industry standards.
In addition to our technical consultant's expertise, our product offers several key advantages:
Comprehensive Processing Capacity: Our manufacturing facilities boast state-of-the-art equipment, including a 5M CNC VTL OPERATOR, 130 & 150 CNC floor boring machines, constant temperature annealing furnace, planer milling machine, CNC machining center, and more, ensuring precision in every detail of production.
Extended Lifespan: The product is designed to last over 40 years, providing a reliable and durable solution for long-term energy needs.
Customer-Centric Site Services: We go beyond product delivery by offering a one-time free site service for customers purchasing three units (capacity ≥100kw) within a year or a total of more than 5 units. This service includes equipment inspection, new site assessment, installation, and comprehensive maintenance training.
OEM Acceptance: Recognizing diverse requirements, we readily accept Original Equipment Manufacturer (OEM) arrangements, tailoring our products to specific needs.
Advanced Manufacturing Processes: Our commitment to quality is evident in our CNC machining, dynamic balance testing, and isothermal annealing processing, ensuring each unit meets stringent standards through Non-Destructive Testing (NDT).
Design and R&D Capabilities: With a team of 13 senior engineers experienced in design and research, we continually innovate to stay at the forefront of technology, offering cutting-edge solutions to our clients.
Product Advantages
1.Comprehensive processing capacity. Such as 5M CNC VTL OPERATOR, 130 & 150 CNC floor boring machines, constant temperature annealing furnace, planer milling machine, CNC machining center ect.
2.Designed lifespan is more than 40 years.
3. Provide one time free site service,if the customer purchases three units (capacity ≥100kw) within one year, or the total amount is more than 5 units. Site service included equipments inspection, new site checking, installation and maintainance training ect,.
4.OEM accepted.
5.CNC machining , dynamic balance tested and isothermal annealing processed,NDT test.
6.Design and R&D Capabilities,13 senior engineers with experienced in design and research.
7.The technical consultant worked on the hydro turbine filed for 50 years and awarded the Chinese State Council Special Allowance.
Suneco proudly presents the 500KW Francis Turbine, combining high-grade quality with a competitive price. As a reputable manufacturer, we prioritize delivering cutting-edge hydroelectric solutions, and our commitment to excellence shines through in this powerful turbine. Designed for optimal efficiency, our competitive pricing ensures accessibility without compromising on performance. Suneco’s dedication to innovation, sustainability, and cost-effectiveness aligns with the global shift towards cleaner and more efficient energy sources. With our 500KW Francis Turbine, clients can harness the power of flowing water confidently, benefiting from a top-tier product at a competitive cost. Francis turbine definition is a combination of both impulse and reaction turbine, where the blades rotate using both reaction and impulse force of water flowing through them producing electricity more efficiently. Francis turbine is used for the production of electricity most frequently in medium or large-scale hydropower stations.